Whether you’re just starting your credit journey or seeking to rebuild from a challenging financial past, arming yourself with the right information can be transformative. By educating yourself on the intricacies of credit scores, credit reports, and responsible financial habits, you gain more than just a temporary fix – you acquire skills that will serve you for a lifetime.
Звукоізоляція від зовнішнього шуму - це те, що ви заслуговуєте. Наші вхідні двері з шумоізоляцією гарантують вам максимальний комфорт та спокій в вашому житті. https://prostroiku.info/vhidni-dveri-z-shumoizolyatsiyeyu-osoblivosti-i-poradi-viboru/
Екологічна дружність: Ми підтримуємо екологічні стандарти виробництва, використовуючи відновлювальні матеріали і екологічно чисті технології. Обираючи наші двері прихованого монтажу, ви дбаєте про навколишнє середовище. https://derevko.com.ua/dveri-pryhovanogo-montazhu-perevagy-u-vykorystanni-ta-vplyv-na-dyzajn-interyeru/
https://zapple.tech/blog/test-automation-methodologies/outsource-software-testing/ Why Outsource Software Testing Is the Best Choice? Revolutionize your software testing approach with Zapple! Discover expert insights on test automation methodologies and the benefits of outsourcing software testing. Streamline your processes, enhance quality, and stay ahead in the competitive market. Explore now!
Идеальное сочетание стиля и функциональности - это то, что делает наши входные двери со скрытыми петлями такими востребованными. Обеспечьте безопасность и элегантность вашему дому с нашими качественными дверями. Придайте своему дому неповторимый шарм. https://vlast.com.ua/ru/dveri-so-skrytymi-petlyami
Discover how Web Test Automation Services are reshaping the landscape of QA processes in our groundbreaking article. From increased efficiency to unparalleled accuracy, witness the revolution firsthand and propel your testing strategy into the future.
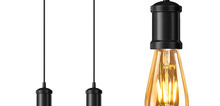
Lighting fixtures are the finishing touch in home decor, playing a pivotal role in shaping the ambiance and comfort of a living space. Hence, many individuals approach the selection of lighting fixtures with great care during home renovation projects. Some with strong DIY skills even enjoy designing and crafting their own lighting fixtures. To embark on a DIY journey, however, it's essential to start with a fully functional base fixture, which saves a lot of hassle and ensures the safety of the fixture. Here, we recommend a best pendant light for DIY. A Versatile Solution Our single pendant light stands out for its minimalist design and limitless customization possibilities. Unlike traditional pendant lights, ours comes without a shade, allowing users to unleash their creativity and customize the appearance according to their taste.
Adjustable Suspension This pendant light features a wire suspension, with a standard 6-foot wire for easy adjustment of the hanging height. Whether your ceiling is high or low, or the installation location varies in height, this pendant light can adapt perfectly, creating the perfect ambiance for any occasion, whether it's a cozy dinner with loved ones or a lively gathering with friends.
Endless Styling Options The main reason why this pendant light is ideal for DIY is its compatibility with various lampshades. With a widely adaptable E26 lamp holder and no included lampshade, you have complete freedom to choose lampshades of any style for pairing. Whether you prefer a modern industrial look, a bohemian chic ambiance, or classic elegance, simply choose a lampshade to transform the style according to your preferences.
Why DIY? So why choose to DIY a pendant light? The answer lies in the freedom it offers. Unlike traditional lighting fixtures, where what you see is what you get, with our pendant light, you become the designer. You have the ability to transform your space and express your personality in ways that pre-made options simply cannot match.
Express Your Creativity DIY is not just about saving money or customizing your space; it's about self-expression. It's about turning a house into a home, infused with your unique vision and personality. With our pendant light, you have the opportunity to unleash your creativity and make a unique statement.
Embrace Sustainability In a world where sustainability is increasingly important, DIY offers a way to reduce waste and minimize environmental impact. By repurposing existing materials or choosing eco-friendly lampshades, you can create a lighting fixture that not only enhances your space but also aligns with your values.
DIY Examples Bohemian Style with Woven Lampshade: When paired with a woven lampshade, this single pendant light instantly transforms into a bohemian-style fixture, adding a touch of coastal charm to your home environment.
Casual Minimalism with Fabric Shade: This pendant light paired with a fabric lampshade exudes casual minimalism, perfect for those who prefer a simple and comfortable decorating style.
Artistic Personality with Colored Glass Shades: This pendant light can be paired with various colorful glass lampshades, adding a touch of personality and artistic style to your home environment. Suitable for those who pursue individuality.
There are many more styles waiting for you to explore. If you also enjoy DIY home lighting, order one today and start your design journey. Shop on Amazon: Mini Pendent Light Easy for DIY Conclusion In conclusion, this pendant light is not just a lighting fixture; it's a canvas waiting to be painted. With its adjustable suspension and compatibility with various lampshades, it offers limitless customization possibilities. So why settle for ordinary when you can create something extraordinary? Choose our pendant light today and unleash your inner designer!
9260 Steel is a metal made by alloying iron with carbon, and it is used in almost every industry thanks to its valuable mechanical properties. Its strength is paired with good workability and machinability, and it is relatively inexpensive to produce, which makes it a primary choice of material for most designers. The American Iron & Steel Institute (AISI) and the Society of Automotive Engineers (SAE) have made steel selection easier by naming different grades of steel with indexes that specify the alloying elements and general properties of the steel. This article will highlight 9260 steel, a high silicon alloy spring steel known for its outstanding working characteristics. By outlining the chemical composition, mechanical properties, and applications of 9260 steel, this article aims to help the reader decide whether 9260 steel is a good material choice for their project.
Physical Properties of 9260 Steel 9260 steel is given its four-digit name by the joint naming index created by the AISI and SAE. To learn more about this naming scheme, as well as the differences between steel grades, review our article on the types of steels.
The first digit designates the class of the steel alloy- that is, what the major alloying components are (besides carbon). For this steel, the “9” shows that this steel is of the silicon-manganese class of alloy steels. The second digit represents the percentage of these major elements; the “2” in 9260 steel, therefore, means this class is around 2% silicon/manganese. Finally, the last two digits represent the carbon percentage in the steel, in increments of 0.01%. Using this rule, 9260 steel is 0.60% carbon. The exact chemical composition of 9260 steel is much more specific, (seen below with tolerances), but its name gives a good idea as to its general makeup.
The specific elemental percentages of 9260 steel are:
0.56- 0.64% Carbon 0.75-1.0% Manganese
Summary This article presented a brief summary of the properties, strength, and applications of 9260 steel. For information on other products, Please visit XTJ.XTJ is a leading 9260 Steel Parts Manufacturer that is dedicated to providing one-stop manufacturing solutions from prototype to production. We are proud to be an ISO 9001 certified system quality management company and we are determined to create value in every customer relationship. We do that through collaboration, innovation, process improvements, and exceptional workmanship.
What is The Plastic Resins for Injection Molding Process? Plastic injection molding is one of the most popular as well as versatile manufacturing techniques. It has multiple advantages like the flexibility of design, the ability to work with multiple plastic resins simultaneously, cost-effectiveness, precision and accuracy of the products, etc.
The technique hence reigns supreme in the world of plastics.
However, the number of plastic polymers invented till date are numerous. With such a wide list to choose from, it can often be overwhelming for manufacturers and designers to choose the best one for a product.
The article here will take you through the common material selection factors as well as the most widely used plastic resins and their benefits. Read on to know more.
Material selection factors Each plastic resin has its own unique properties. It is important to consider the defining properties of each to choose the right one for your product. It is also noteworthy that resin properties are also often enhanced by the use of fillers like silica, calcium carbonate, mica, alumina trihydrate, glass, clay, etc. Following are the key properties that need to be considered for each plastic resin before making a selection for the plastic injection molding process:
Hardness Hardness, also popularly referred to as Shore hardness is used to measure the hardness/stiffness of the plastic resin. Hardness is basically the measure of resistance to indentation for a particular plastic resin. It is measured on the Durometer scale.
Various products have different levels of hardness requirements when it comes to plastics. Before moving on to plastic injection molding, it is important for the manufacturer to choose the appropriate type of plastic for a particular product and design.
Picking the right material means considering its usage environment, abrasion levels, as well as the purpose of the product. Plastic resins like HDPE (High-Density Polyethylene), PVC are on the softer side of the scale and are suitable for products that need soft feel. Others like PP (Polypropylene), Nylon are of moderate softness/hardness whereas those like ABS(Acrylonitrile Butadiene Styrene) and PC(Polycarbonate) are considered for hard applications.
Flexibility Material flexibility is another very important parameter that needs to be considered for product applications. Flexibility is defined as the ability of a material to bend without breaking.
It is also noteworthy to mention that flexibility is not necessarily similar to softness. Various plastic resins that are ranked as soft (like Nylon) on the Durometer scale are not flexible and break easily when stress/load is applied to it. ABS, on the other hand, is a hard plastic but is considerably flexible.
Multiple industrial applications have requirements for plastics that are sufficiently hard/durable and yet flexible. It is important to consider all the properties of a plastic resin before making a final choice for a product.
Weight The weight of a plastic resin material plays a very vital role in its selection for different applications. The weight of plastic resin is determined by the density of the plastic polymer.
Polypropylene (PP), High-Density Polyethylene (HDPE) and Acrylonitrile Butadiene Styrene (ABS) are considered as lightweight plastics. On the other hand, PVC, Polycarbonate (PC) are considered heavy.
Cost This is again a very critical important factor for plastic injection molding. That said, it is more important to consider the other properties of a plastic resin suitable for a particular application before cost.
Cost of different plastic resins used for plastic injection molding varies based on availability, ease of production, polymer properties, etc. Plastic resins like HDPE, PP, and ABS are relatively less costly than resins like Nylon, PC, etc.
– Various other factors that are considered before selection of a plastic resin include the impact strength, tensile strength, elasticity, chemical resistance, heat deflection/tolerance, and water absorption.
Most widely used plastic resins With hundreds of existing as well as emerging resins in the market, it can often be overwhelming to select a particular plastic resin for plastic injection molding. However, the process is not as daunting as it seems.
XTJ is a leading OEM Manufacturer that is dedicated to providing one-stop manufacturing solutions from prototype to production. We are proud to be an ISO 9001 certified system quality management company and we are determined to create value in every customer relationship. We do that through collaboration, innovation, process improvements, and exceptional workmanship.
try
Each plastic resin has its unique properties, advantages as well as disadvantages. Following are some of the most commonly used resins for plastic injection molding:
- Acrylonitrile Butadiene Styrene (ABS) ABS is a very popular plastic in the world of injection molding. With its superior properties like toughness, impact resistance, heat resistance, durability, strength, the resin finds its applications in multiple industries.
Its lightweight and strength make it a popular choice for the automotive industry. Since ABS has combined strengths of both acrylonitrile and styrene polymers, it is a perfect fit for applications which require toughness of the material.
ABS can also be easily molded into desirable shapes and offers glossy effects with a superior finish quality.
Other properties of ABS like easy adhering to itself and other similar plastics makes it a good choice for co-injection molding. Additionally, the adhering properties of ABS make it great for metal coatings.
plastic resins
ABS plastics find their use in multiple applications like appliances, computer parts, housing equipment, sports and musical instruments, medical devices, helmets, toys, electronics, automobiles, etc.
- Low-Density Polyethylene (LDPE) and High-Density Polyethylene (HDPE) LDPE is one of the most flexible types of plastic resins available. It is widely used for its superior moisture resistance properties, chemical resistance, impact strength, as well as cost-effectiveness.
Various applications of LDPE include household goods, medical products, electrical wirings, computer components, food industry (like juice boxes), toys, agricultural products, furniture, compost bins, etc. That said, LDPE has low-temperature resistance and is not suitable for high-temperature environments.
HDPE, on the other hand, has a higher impact resistance, moisture resistance, heat resistance, tensile strength, and ductility. Additionally, HDPE is a food-grade plastic and is hence a preferred resin when it comes to food packaging materials.
These plastics are hence used in applications where more strength, rigidity and heat resistance is required. Applications that make use of HDPE are kitchenware, refrigerator shelves, plastic bags, plastic containers, water bottles, etc.
Plastic water bottles
HDPE is not just inexpensive to start with but also 100% recyclable which makes it a highly cost efficient plastic resin.
- Polycarbonate (PC) Polycarbonates are extremely hard and strong plastics and provide extremely high impact resistance. Additionally PC plastic resins are transparent and amorphous and are used in applications where transparency and strength are required together.
plastic resins car stereo PC plastic resins are commonly used to manufacture bulletproof glass. Other uses of PC are in the manufacture of eyeglasses, lenses, medical devices, mobile phones, DVDs and car parts.
- Polyamide (Nylon) Polyamide or Nylon finds its usage in a large range of sectors. This plastic resin comes with superior properties like toughness, chemical, and electrical resistance, wear resistance as well as stability.
Nylon polymers offer resistance to rugged environments that bring in abrasion, high impact or chemical contacts.
Polyamide or Nylon plastic resin is used largely in the production of medical parts, automotive industry, sports gear, and other industrial tools and equipment.
- High Impact Polystyrene (HIPS) HIPS resin offers good dimensional stability, impact resistance and customizable surfaces which are easy to decorate. Applications which require printing, use of glues and decoration parts, etc use HIPS.
Applications like display boards, garden equipment, packaging material, TV parts, toys, cold drink cups, computer housings, etc utilize HIPS. It is also highly utilized in graphic arts as well as digital printing equipment.
HIPS is also very cost-efficient which makes it a preferred choice for various applications.
XTJ is a leading OEM Manufacturer that is dedicated to providing one-stop manufacturing solutions from prototype to production. We are proud to be an ISO 9001 certified system quality management company and we are determined to create value in every customer relationship. We do that through collaboration, innovation, process improvements, and exceptional workmanship.
try
- Polypropylene (PP)
PP is perhaps the most used plastic resins globally. The plastic has good chemical and electrical resistance, hardness, high melting point, stress resistance as well as high elasticity. Further, it is also highly valued for its insulation properties.
Various fillers are added to customize the plastic resin to add more strength to it. The additives lend further strength to the plastic (thereby known as the steel of the plastics)
Its diverse applications include electrical equipment, household appliances, automotive industry, packaging materials, construction purposes, etc.
PP is particularly preferred in the food and beverage industry since the polymer does not leach chemicals and is considered safe for food products.
It is also used in combination with other plastics to create kitchen and tableware, toys, medical components, washing machine buckets, etc.
plastic resins plastic resins for medical parts Similar to acetal, it also offers properties of minimizing friction and is used in point of contact applications.
- Acrylic (PMMA) Poly(methyl methacrylate), popularly known as Acrylic or PMMA is a widely used plastic resin, especially in applications where substitutes for glass are needed.
It’s properties like transparency, chemical resistance, hardness, impact resistance, dimensional stability make it a preferred choice for a wide range of applications that are manufactured using plastic injection molding technique.
Additionally, acrylic is a very low-cost plastic resin and is easily available.
Acrylic is a transparent and moldable plastic used in the preparation of windows, car screens, picture frames, beauty products, paints, eye lenses, etc.
- Polyetheretherketone (PEEK) PEEK is a very widely used high-performance plastic that offers extreme resistance to even the harshest of chemical attacks. Additionally, the plastic resin is resistant to thermal and aqueous degradation.
The high strength and robust properties of PEEK make it suitable for various applications like piston parts, compressor plates, pumps, etc. Its chemical resistance properties make it a good choice for use in liquid chromatography columns and other parts used in chemical processing industries.
Additionally, it is also being highly used in sectors like the automotive industry, aerospace and even in medical parts (like implants).
- Acetal/ Polyoxymethylene (POM) Acetal or polyoxymethylene is popular for its outstanding properties like hardness, wear resistance, chemical resistance, etc. Additionally, the plastic resin has good colorization properties, low moisture absorption as well as good heat distortion.
Acetal is a great choice in applications where dimensional stability, as well as friction resistance, is required. This plastic resin is widely used in the food and beverage industries. Additionally, it is used for other sectors like the automotive industries, household appliances, plastic gears, etc.
Its properties of minimizing friction make it an excellent choice for point of contact applications like guitar picks, buckles, pumps and valve parts, fixtures, etc.
- Thermoplastic Polyurethane (TPU) The soft and elastic properties of TPU make is an ideal choice for products that require rubber-like elasticity. Additionally, the high tensile strength, as well as the ability to withstand high temperatures, makes it a good choice for applications like cable insulations, electrical tools, sports gear, etc.
Choosing the right material for creating a part using plastic injection molding technique is absolutely essential for optimal performance. And that’s not the only reason to do so. It saves a good amount of time as well as money spent during the manufacturing process.
The huge range of plastic resins available opens up doors for unlimited plastic molding opportunities and designs. However, it is important to understand that all applications have different material needs when it comes to injection molded plastics.
Phosphor Bronze has come a long way from just being an alloy of copper and tin; it is now a broader class of copper alloys that are still finding new uses to this day. The diversification of bronze can make material selection difficult, however, so this article will help alleviate some confusion by exploring one kind of bronze, the phosphor bronzes. By examining the physical, chemical, and mechanical properties of phosphor bronze, this article aims to help interested designers Phosphor Bronzedetermine if this copper alloy will be applicable to their projects. We will first examine the composition of phosphor bronze, and then discuss its strengths, drawbacks, mechanical properties, and finally common applications of such a useful metal.
Physical Properties of Phosphor Bronze It may be helpful to review our article on the types of bronzes, so as to understand the commonalities between copper alloys and their popular applications.
Below, in Figure 1, is a qualitative chart depicting the composition of phosphor bronze:
Pie chart representation of the material composition of phosphor bronze. Figure 1: Qualitative breakdown of phosphor bronze. Notice how the included zinc, iron, lead, and phosphorus percentages are infinitesimal. From examining Figure 1, it may be difficult to understand why phosphor bronze is named as such when it is mainly an alloy of copper and tin. This is because it only takes a small percentage of phosphorus, around 0.03-0.035% by weight, to imbue these alloys with unique properties such as improved flow, wear resistance, and stiffness. They are also known as tin bronzes, but always have some amount of phosphorus present to be truly considered a phosphor bronze. Their density is around 8.8 g/cm3, and most forms of these alloys respond to hot working, cold working, and heat treatment. They are exceptionally elastic in nature, resistant to fatigue and corrosion, and are readily formable, castable, and solderable. The addition of lead will make phosphor bronzes stronger and more machinable, but unleaded phosphor bronzes are also strong and resistant by themselves. They are most often used for corrosion-resistant applications, as well as in other applications that need a springy-yet-durable material.
Resistances and weaknesses Most phosphor bronze alloys are tarnish and corrosion resistant, making them useful in electrical conduit and other caustic environments. They are also resistant to fatigue, meaning they retain their strength over many cycles of loading. The addition of tin will increase this resistance along with its strength, and the addition of lead will make a phosphor bronze that is colloquially known as the “Machinist’s friend” (alloy COLPHOS 90/C54400), as it is nearly indistinguishable from free-cutting brass alloys. Most alloys form an attractive patina in the presence of oxygen and are therefore also useful for decorative applications. Phosphor bronze’s main disadvantages can be its lower electrical conductivity, as phosphorus will reduce the ability of the metal to conduct current, and its price tag. The dust and fumes of phosphor bronze are also toxic when inhaled, so be wary of both your wallet and your lungs.
Mechanical Properties For Phosphor Bronze Table 1, below, shows some mechanical properties relevant to phosphor bronze’s uses and strengths. This section will briefly explain each property and show how they make this copper alloy unique.
Table 1: Summary of mechanical properties for phosphor bronze – note that this table is only a general summary and not a de-facto list of properties for all phosphor bronzes. Note: This table is only a general summary and not a de-facto list of properties for all phosphor bronzes. Mechanical Properties
Metric
English
Tensile yield strength
380-450 MPa
55100-65260 psi
Modulus of Elasticity
110 GPa
16000 ksi
Electrical conductivity (relative to pure copper)
15%
Hardness (Rockwell B)
75-85
Machinability
20-100%
Tensile yield strength is a stress value that determines the point after which the material will plastically deform. It is a common measure of a material’s non-yielding strength, as stress below this point will not bend or stretch the alloy (though, there are always exceptions). It is a useful measure for fabricators when machining, as well as in applications where the material must keep its form without jeopardizing the structure’s integrity. Phosphor bronze has an impressive yield strength, matching some aluminum alloys and surpassing even other bronzes, and this is thanks to its high percentage of tin and phosphorus. When combined with its good spring characteristics, this creates an alloy that is strong and will stay strong.
Modulus of elasticity, or Young’s modulus, describes the ability of a material to elastically deform- that is, how stiff a material is. Counterintuitively, a higher Youngs modulus suggests a more elastic material, but this is not a measure of “stretchiness”; it is a measure of internal material strength and how likely the material is to return to its original shape in the presence of an increasing force. A high Youngs modulus, therefore, means a generally strong material as it will not plastically deform under increasing loading conditions. Phosphor bronze has a decently high elastic modulus (almost half that of most steels), which suggests it is not as strong as other alloys but can hold its own under moderate conditions. This causes phosphor bronze to be both useful for shaping operations and more difficult to machine, but more on this in a bit.
The electrical conductivity of phosphor bronze is about 15% that of pure copper – so why use it in electrical applications when copper is better able to carry electricity? The answer lies in phosphor bronze’s good balance of fatigue strength, corrosion resistance, and electrical conductivity. While not a standout alloy in any one of these categories, its ability to be both resistant, strong, and conductive means electrical components made from phosphor bronze will last longer than copper analogs. Therefore, phosphor bronze has been used for a long time as a material in electrical switches, fasteners, connectors, and more, as it can bare both mechanical and electrical loads better than typical copper counterparts.
Material hardness is always relative to some standard hardness machine, and the various hardness scales provide a comparative list of materials within the same general class/material. Table 1 shows hardness values from the Rockwell B scale, which is often used to describe the hardness of copper alloys and other metals. Materials with lower hardness values are generally softer, meaning they are more easily scratched, dented, and locally deformed on their surface, while higher numbers suggest a material that is difficult to scratch (think borosilicate glass, ceramic, etc.). For reference, the Rockwell B hardness of copper is around 50, so it is clear from Table 1 that phosphor bronze is more scratch-resistant than its pure form. It is also not as strong as other, more harden-able alloys such as steel, which can be good or bad depending upon the application. For example, if etching and inlay is part of your application, phosphor bronze may be a good balance between strength and workability, but this is dependent upon the specific alloy type and strengthening procedures.
Like hardness, machinability is a comparative measure of a material’s ability to be machined and is always in reference to some standard machining material (for the bronzes, this material is UNS C36000 – free cutting brass). This standard material is given a machinability score of 100%, meaning it is easy to machine and causes little problems in the shop. Alloys compared to this reference with a score lower than 100% are more difficult to machine, and this is generally the case with phosphor bronzes; however, phosphor bronze can be specially made to address these concerns (along with most other alloys, depending upon your source). Phosphor bronze can be bought with increased lead levels that will remove its machining difficulty, as it becomes more self-lubricating. So, while most phosphor bronze alloys are somewhat difficult to mill, this issue can be addressed with the right alloy selection.
Applications of Phosphor Bronze Phosphor bronze has been used for many years in electrical components, but it is still finding new uses thanks to technological advances and the demand for more specialized materials. Below is a list of phosphor bronze applications but know that it has many uses outside of this list, and new applications are still being developed.
Some common applications include:
Springs Sleeve bushings & bearings Welding rods Jewelry Guitar strings Dental bridges and more.
Phosphor bronzes meets many designer specifications and is a proven engineering material. If it sounds attractive to your application, be sure to contact your supplier, as they will have the newest alloys available.
XTJ is a leading OEM Manufacturer that is dedicated to providing one-stop manufacturing solutions from prototype to production. We are proud to be an ISO 9001 certified system quality management company and we are determined to create value in every customer relationship. We do that through collaboration, innovation, process improvements, and exceptional workmanship.